Wood veneer is not just a material—it’s a timeless expression of craftsmanship and design philosophy. In modern construction, furniture production, and architectural applications, the use of high-grade wood veneer elevates projects with warmth, authenticity, and sustainability. Whether you are crafting luxury interiors or designing weather-resistant facades, wood veneer opens up a world of possibilities while maintaining cost efficiency and environmental responsibility.
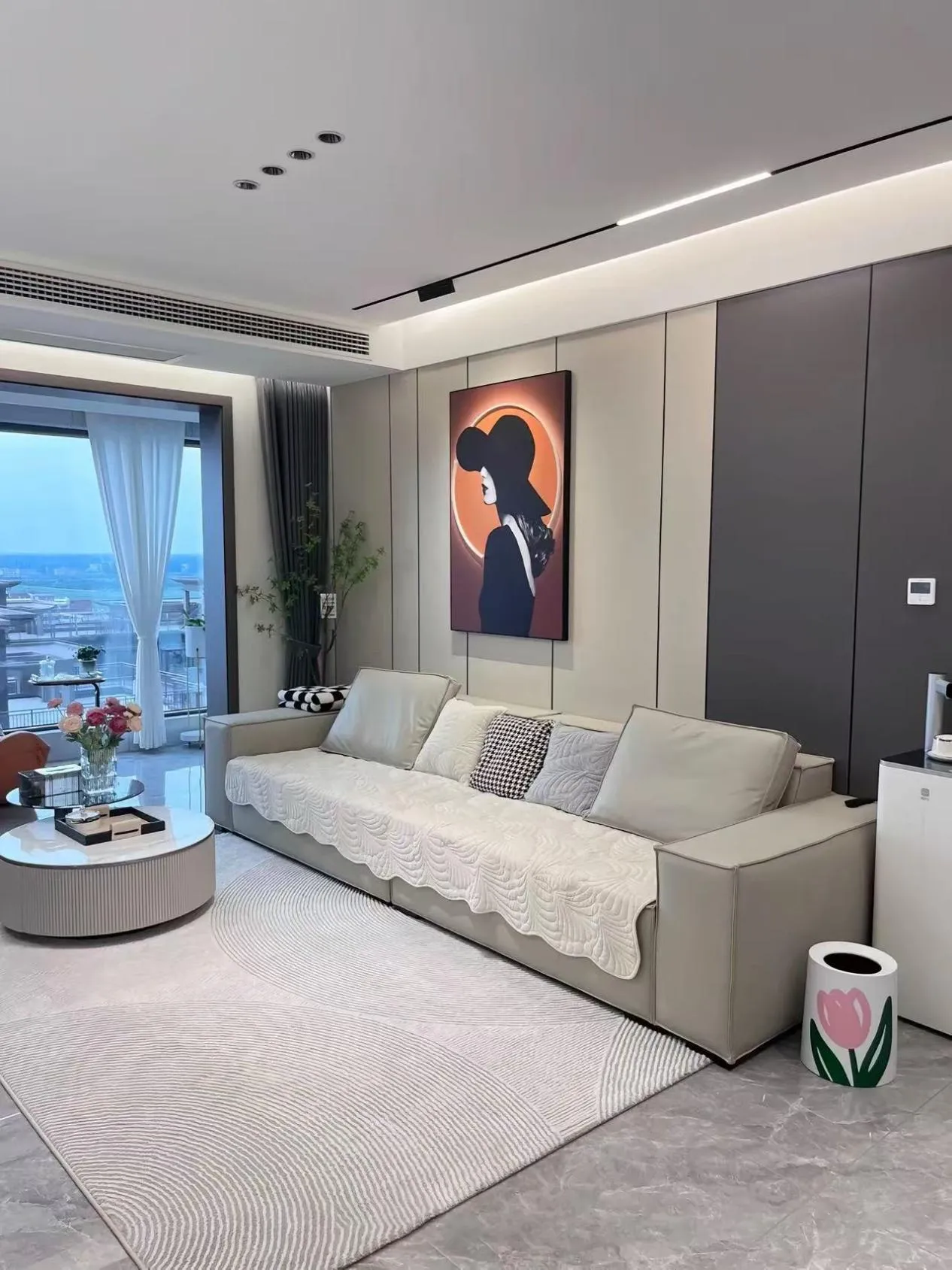
Interior Sophistication Enhanced by Exotic Wood Veneer Sheets in Architectural Design
For architects and interior designers, selecting the right surface material is crucial. Incorporating exotic wood veneer sheets in interiors introduces a rare combination of aesthetic uniqueness and practical performance. These sheets, sourced from rare or non-native species, offer intricate grains and rich colors that mass-produced alternatives simply cannot match. From wall panels in executive offices to cabinetry in luxury yachts, exotic veneers lend a touch of refinement and exclusivity. The variety in texture, tone, and figure allows designers to achieve their vision without compromising on sustainability or natural beauty.
Creating Lasting Impressions with Durable Exterior Wood Veneer Applications
While veneer has long been associated with indoor aesthetics, innovations in treatment and substrate bonding have brought exterior wood veneer into the spotlight. These veneers are engineered for weather resistance, UV stability, and long-term structural integrity, making them ideal for outdoor applications such as soffits, exterior cladding, and facade accenting. When properly treated, these veneers resist warping, cracking, and fading—ensuring that their visual appeal matches their durability. Architects now rely on exterior veneer not only for performance but to integrate natural textures into urban environments.
Architectural Ambitions Realized with Exterior Wood Veneer Panels for Cladding
Designers seeking a seamless blend of form and function often turn to exterior wood veneer panels. These ready-to-install panels combine veneer aesthetics with stable, engineered backing materials that can endure a variety of climates. The panel format simplifies installation and improves structural performance while offering creative flexibility in dimensions, finishes, and grain orientation. From residential houses to commercial buildings, exterior veneer panels transform blank surfaces into living, breathing expressions of wood’s natural elegance, without the excessive weight or instability of solid timber.
Manufacturing Excellence Begins with Face Veneer for Plywood Applications
In plywood production, the visual and functional quality of the topmost layer is paramount. The use of face veneer for plywood ensures a flawless surface finish that’s both attractive and suitable for high-end furniture, cabinetry, and architectural detailing. These veneers are selected based on grain uniformity, minimal defects, and optimal color matching. Their thinness allows them to adhere tightly to plywood cores while providing a hardwood surface layer that mimics solid wood in both appearance and touch. By choosing premium face veneers, manufacturers elevate their plywood from commodity to quality-tier product.
Face Veneer Plywood Offers a Balance Between Strength, Beauty, and Cost-Efficiency
Consumers and builders alike are turning toward face veneer plywood as a sustainable and economical alternative to solid wood. These plywood panels consist of high-grade face veneers bonded to core layers of lower-cost or recycled wood materials. The result is a sheet that combines the visual appeal of hardwood with the structural advantages of engineered products. Perfect for doors, furniture, and shelving, face veneer plywood balances weight, cost, and durability—without sacrificing aesthetics. Its smooth finish also makes it an ideal substrate for staining or varnishing, further enhancing its versatility.
How Is Exotic Veneer Sourced and Certified?
Ethical sourcing is essential when using exotic wood veneer. Most reputable suppliers provide certification from organizations like FSC (Forest Stewardship Council) to ensure the wood is harvested sustainably and legally, promoting biodiversity and forest regeneration.
Can Exterior Veneer Withstand Harsh Weather?
Yes. Advanced sealing, UV inhibitors, and water-resistant adhesives allow exterior wood veneers and panels to perform reliably in outdoor settings, including rain, heat, and freezing temperatures. Regular maintenance enhances their longevity even further.
What’s the Difference Between Face Veneer and Core Veneer in Plywood?
Face veneer is the topmost layer visible in finished plywood products and is selected for its appearance, while core veneer makes up the internal structure. The quality of face veneer directly impacts the aesthetics and finishability of plywood panels.
Wood Veneer Solutions FAQs
Q: What are the benefits of using exotic wood veneer sheets over domestic veneers?
A: Exotic veneer sheets offer a more diverse range of grain patterns and colors, providing unique and upscale aesthetics for luxury projects without requiring solid hardwood usage.
Q: How durable is exterior wood veneer in commercial installations?
A: When properly installed and maintained, exterior veneers resist UV damage, moisture infiltration, and delamination, making them suitable for facades, ceilings, and outdoor furniture.
Q: Are exterior wood veneer panels easy to install?
A: Yes. They are typically pre-laminated onto stable backer boards, allowing for rapid installation via mechanical fasteners or adhesives. This reduces labor time and ensures uniform finish quality.
Q: How is face veneer for plywood selected in manufacturing?
A: Manufacturers grade face veneers based on visual perfection—grain symmetry, color consistency, and absence of knots or blemishes. These veneers undergo precision slicing and drying before application.
Q: Why choose face veneer plywood instead of solid hardwood panels?
A: Face veneer plywood offers the look of solid wood at a lower cost and reduced weight. It’s less prone to warping, easier to handle, and consumes less natural resources during production.