In today’s construction and furniture industries, selecting the right material is crucial to achieving both longevity and aesthetic appeal. Wood-based panels have evolved far beyond traditional solid wood, offering innovative options like UV board material and engineered wood substrates that combine strength with versatility. Whether you are an architect, furniture designer, or DIY enthusiast, understanding these materials can guide you to smarter choices that blend cost efficiency with performance.
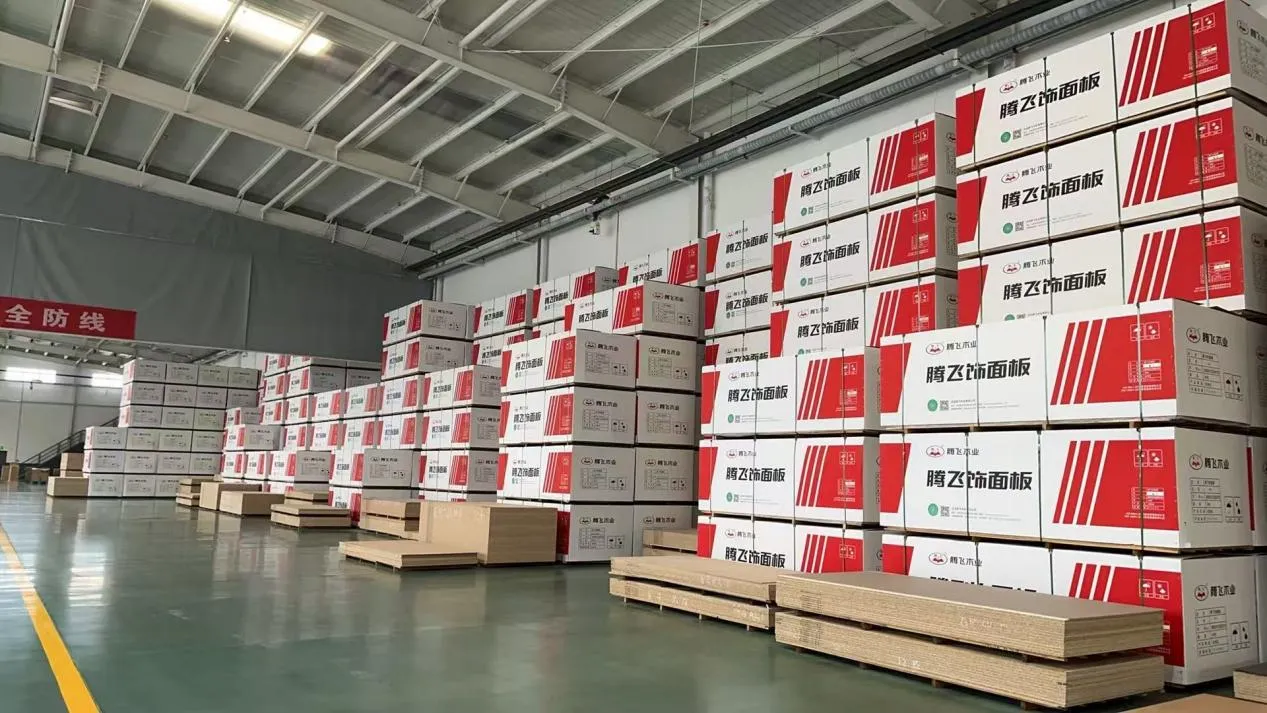
Comparing Strength and Surface Quality in UV Board Material Options
Among the popular choices for surfaces that demand durability and a flawless finish, UV board material stands out due to its high resistance to scratches, moisture, and fading. This material undergoes a curing process with ultraviolet light, which bonds resins and coatings firmly onto the surface, creating a sleek and tough finish. Unlike traditional painted or laminated wood panels, UV board material maintains its appearance even under heavy use, making it ideal for kitchen cabinets, office furniture, and commercial interiors. While the initial price point may be slightly higher, the reduction in maintenance and replacement costs offers considerable long-term value.
Exploring the Role of Wood Substrate in Composite Panel Manufacturing
The foundation of many modern engineered wood products lies in the wood substrate, which serves as the core layer supporting surface finishes and laminates. What is wood substrate often depends on the type of fibers or particles used, such as particleboard, MDF, or plywood. This core material must balance structural integrity with compatibility to decorative layers, making it a key consideration in producing furniture, flooring, and wall panels. A well-chosen wood substrate ensures the final product withstands physical stress while maintaining a lightweight profile.
Budgeting Wisely by Understanding MDF Wood Cost Variables
For contractors and hobbyists alike, knowing the MDF wood cost is critical for accurate project budgeting. The price of MDF varies widely based on thickness, density, supplier, and treatment processes such as moisture resistance or fire retardancy. While MDF tends to be more affordable than solid wood or HDF, hidden costs can arise from additional finishing, cutting, and installation requirements. Therefore, comparing MDF wood cost alongside expected performance and longevity can prevent overspending on materials that may not meet project demands.
What Makes UV Board Material Ideal for Commercial Applications?
UV board materials offer superior surface durability and low maintenance, perfect for environments like offices and retail spaces where frequent cleaning and heavy use occur. Their resistance to discoloration and abrasion keeps interiors looking fresh longer.
Wood-Based Materials FAQs
Q: How does UV board material differ from regular laminated boards?
A: UV board material undergoes curing with ultraviolet light, creating a tougher and more resistant surface than conventional laminated boards, which improves durability and aesthetics.
Q: What are the main considerations when choosing between HDF v MDF?
A: Project requirements such as load-bearing capacity, moisture exposure, and finishing needs determine whether HDF or MDF is more suitable.
Q: What exactly is MDF made from?
A: MDF consists of wood fibers bonded with resin under heat and pressure, forming a uniform panel used widely in woodworking.
Q: What role does wood substrate play in engineered panels?
A: The wood substrate forms the core that supports decorative surfaces, influencing strength, weight, and stability.
Q: Is MDF wood cost justified given its performance?
A: Yes, MDF provides a cost-effective, versatile solution, especially when factoring in ease of finishing and availability.